
In modern manufacturing, titanium and titanium alloys have been widely used in many key fields such as aerospace, medical, and automotive due to their excellent properties, such as high strength, low density, excellent corrosion resistance, and high temperature resistance. From key components of aircraft engines to medical devices implanted in the human body, titanium parts play an indispensable role. However, these excellent properties also make titanium materials face many challenges in the processing process. Traditional processing methods often fail to meet the processing requirements of high precision, high efficiency, and high quality. The emergence of numerical control (CNC) technology provides an effective solution for the processing of titanium parts. It can achieve precise processing of complex shapes, improve processing efficiency and product quality, and reduce production costs. Therefore, in-depth understanding and mastering of the technology and process of CNC machining titanium parts is of great significance to improving the overall level and competitiveness of the manufacturing industry.
1. Characteristics and Classification of Titanium and Titanium Alloys
1.1 Characteristics
Physical Properties:
The density of titanium is about 4.51g/cm³, which is only about 60% of steel, which makes it very advantageous in applications with strict weight requirements, such as aerospace. Titanium has a melting point of up to 1668℃ and has good high-temperature properties. It can still maintain high strength and stability at high temperatures. In addition, titanium has a low thermal expansion coefficient of about (8.2 – 9.4)×10⁻⁶/℃, which means that its size changes less when the temperature changes, and is suitable for precision parts with high dimensional accuracy requirements.
Chemical Properties:
Titanium has excellent corrosion resistance. In most environmental media, such as seawater, oxidizing acids, wet chlorine, etc., a dense and stable oxide film can be quickly formed on the surface of titanium. This oxide film can effectively prevent further corrosion, making it widely used in corrosive environments such as marine engineering and chemical industry. However, at high temperatures, the chemical activity of titanium is enhanced, and it is easy to react with gases such as oxygen, nitrogen, and hydrogen, resulting in deterioration of material properties. Therefore, the environmental atmosphere needs to be strictly controlled during processing and heat treatment.
Mechanical Properties:
Titanium alloys have a high strength-to-weight ratio, and their strength is comparable to that of high-strength steel, while having a lighter weight. For example, the commonly used TC4 titanium alloy (Ti-6Al-4V) has a tensile strength of more than 900MPa. However, the elastic modulus of titanium alloy is low, about 100-120GPa, which is only about half of that of steel, which makes it easy to produce elastic deformation during processing, affecting the processing accuracy. In addition, titanium alloy also has high yield strength and good fatigue performance, suitable for parts subjected to alternating loads.
1.2 Classification
1. Industrial Pure Titanium:
Industrial pure titanium can be divided into three grades: TA1, TA2 and TA3 according to its impurity content. With the increase of grade, the impurity content gradually increases, and the strength and hardness also gradually increase, but the plasticity and toughness decrease accordingly. Industrial pure titanium has good processing performance and corrosion resistance, and is often used to manufacture parts with low strength requirements in the fields of chemical equipment, medical equipment, architectural decoration, etc.
2. α-type Titanium Alloy:
α-type titanium alloy is an alloy based on α-phase solid solution, and its main alloying elements are aluminum, tin, zirconium, etc. This type of alloy has good high temperature strength, oxidation resistance and welding performance, but low room temperature plasticity. Common α-type titanium alloys include TA7 (Ti-5Al-2.5Sn), etc., which are often used to manufacture compressor blades, disks and structural parts of aircraft engines working at high temperatures.
3. β-type Titanium Alloy:
β-type titanium alloy is an alloy based on β-phase solid solution, and its alloying elements are mainly molybdenum, vanadium, niobium, etc. β-type titanium alloy has high strength, good plasticity and machinability, and can be strengthened by heat treatment. However, due to its high content of alloying elements, the cost is relatively high. Typical β-type titanium alloys include TB2 (Ti-5Mo-5V-8Cr-3Al), etc., which are often used to manufacture parts with high strength and toughness requirements in the aerospace field, such as landing gear parts.
4. α + β Titanium Alloy:
α + β titanium alloy is an alloy containing both α phase and β phase. It combines the advantages of α and β titanium alloys and has good strength, plasticity, toughness and processing performance. Its alloying element content is moderate and the cost is relatively low. The most commonly used α + β titanium alloy is TC4 (Ti – 6Al – 4V), which is widely used in aerospace, automotive, medical and other fields, such as manufacturing aircraft fuselage structural parts, engine parts, automotive parts and artificial joints.
2. CNC Milling Titanium Parts
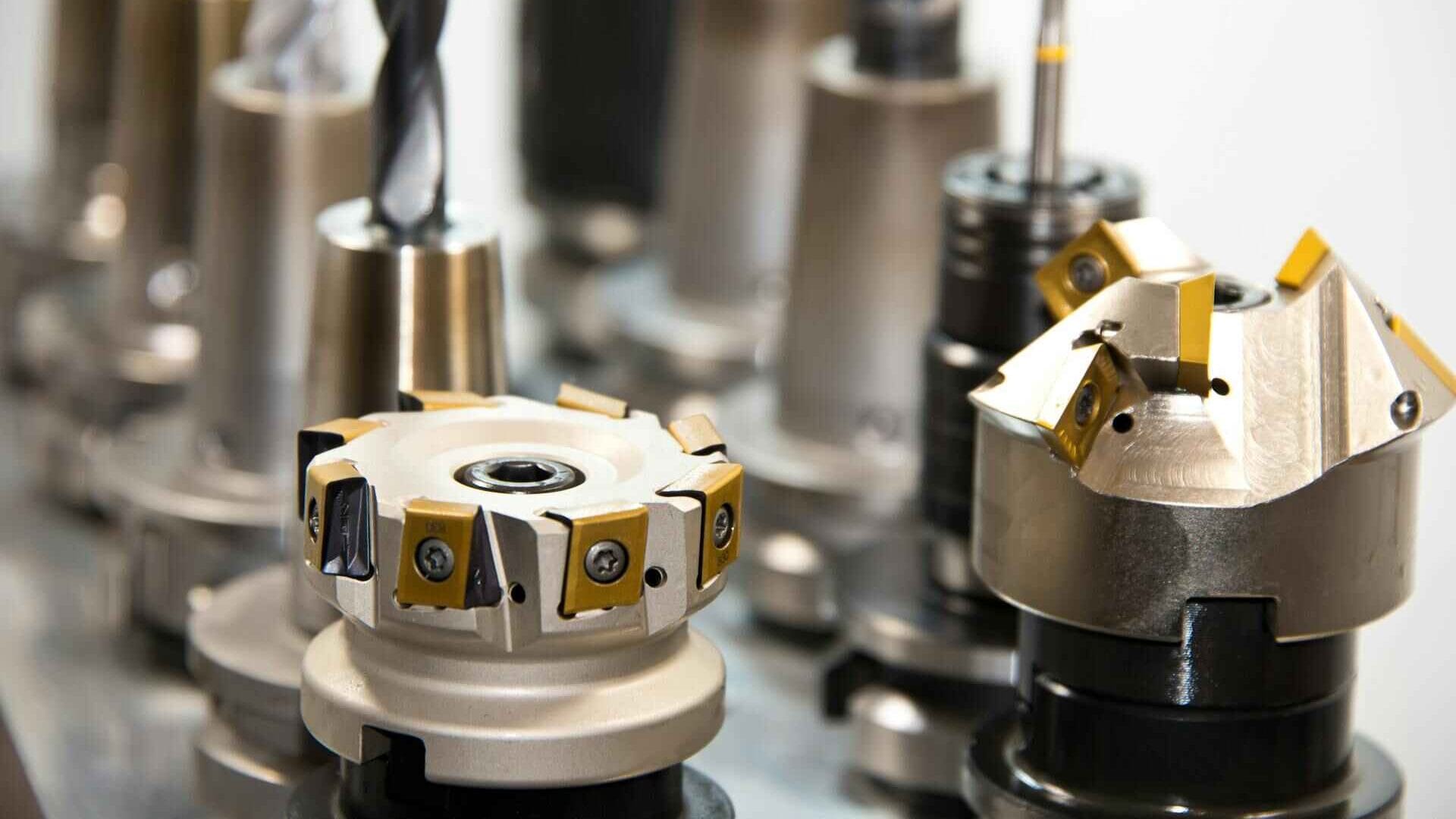
2.1 Tool selection
Tool Material:
When CNC milling titanium parts, the choice of tool material is crucial. Carbide tools are commonly used, among which tungsten-cobalt (YG) carbide performs better in titanium alloy milling due to its higher toughness and wear resistance. For example, carbide tools of grades such as YG8 and YG6X are suitable for roughing and semi-finishing; while for finishing, grades such as YG3X with lower cobalt content and higher hardness can be selected. In addition, coated tools are also an effective means to improve milling performance. For example, TiAlN (titanium aluminum nitride) coated tools have high hardness, oxidation resistance and thermal stability, which can significantly improve the service life and processing efficiency of tools. At high temperatures, TiAlN coating can form a stable protective film, reduce friction and adhesion between the tool and the workpiece, and reduce cutting force and cutting temperature.
Tool Geometry Parameters:
The geometry parameters of the tool have an important influence on the milling process and processing quality. For milling titanium parts, the rake angle of the tool is generally small, usually between 5°-10°, to enhance the strength of the blade and prevent blade breakage during cutting. The back angle is generally 8°-12° to reduce friction and wear between the back face of the tool and the machined surface of the workpiece. The helix angle can be selected from 30° to 45°. A larger helix angle can make the cutting edge gradually cut in and out of the workpiece, reduce the fluctuation of cutting force, and improve the stability of the cutting process. The blunt radius of the cutting edge of the tool should also be properly controlled, generally between 0.05 and 0.1mm. Too large will increase the cutting force, and too small will easily lead to increased blade wear.
2.2 Cutting Parameter Optimization
Cutting Speed:
Due to the poor thermal conductivity of titanium alloy, excessive cutting speed will cause the cutting temperature to rise sharply, accelerate tool wear, and even cause tool breakage. Therefore, when milling titanium parts, the cutting speed is generally low. For rough machining, the cutting speed is usually between 50 and 100m/min; for fine machining, the cutting speed can be controlled between 30 and 80m/min. For example, when using carbide tools to mill TC4 titanium alloy, the cutting speed for rough machining can be selected at about 80m/min, and for fine machining, it can be selected at about 50m/min.
Feed Rate:
The selection of feed rate should comprehensively consider the tool durability, machining surface quality and machining efficiency. Too large feed rate will increase the cutting force, resulting in increased tool wear and reduced machining surface quality; too small feed rate will reduce machining efficiency. Generally speaking, the feed rate can be between 0.1-0.3mm/z during rough machining, and the feed rate can be controlled between 0.05-0.15mm/z during fine machining. For example, when milling a titanium alloy plane, the feed rate can be selected as 0.2mm/z for rough machining and 0.1mm/z for fine machining.
Cutting Depth:
The cutting depth is mainly determined by the machining allowance of the part and the strength of the tool. Under the premise of ensuring the strength of the tool and the machining quality, a larger cutting depth should be selected as much as possible to reduce the number of passes and improve machining efficiency. For rough machining, the cutting depth can reach 1/3-1/2 of the tool diameter; for fine machining, the cutting depth is generally between 0.1-0.5mm. For example, when milling TC4 titanium alloy parts, if a milling cutter with a diameter of 10mm is used for rough machining, the cutting depth can be selected as 3-5mm; the cutting depth can be selected as 0.2mm for fine machining.
2.3 Milling Strategy
Down Milling and Reverse Milling:
In down milling, the movement direction of the tool cutting edge is the same as the workpiece feed direction, and the cutting thickness gradually decreases from the maximum to zero; in reverse milling, the movement direction of the tool cutting edge is opposite to the workpiece feed direction, and the cutting thickness gradually increases from zero to the maximum. When milling titanium parts, due to the low elastic modulus of titanium alloy, the workpiece is prone to elastic deformation. In reverse milling, the impact force when the tool cuts into the workpiece is large, which can easily cause tool vibration and increased wear. Therefore, down milling is generally preferred. Down milling can make the cutting process smoother, reduce tool wear, and improve the quality of the machined surface. However, in some cases, such as when there is a hard skin on the surface of the workpiece blank or the machining allowance is uneven, reverse milling can be used to protect the tool.
Layered Milling:
Due to the large cutting force of titanium alloy, excessive milling depth at one time can easily lead to tool damage and reduced processing accuracy. Therefore, when processing deeper cavities or contours, the strategy of layered milling is usually adopted. Layered milling can decompose a large cutting depth into several smaller cutting depths, and perform milling one by one, thereby reducing the cutting force and ensuring the stability of the processing process. The cutting depth of each layer should be reasonably determined according to the diameter, strength and characteristics of the tool material, and generally should not exceed 1/3 of the tool diameter. For example, when milling a titanium alloy cavity with a depth of 30mm, if a milling cutter with a diameter of 16mm is used, the cutting depth of each layer can be set to 5mm, and milling can be performed in 6 layers.
Contour Milling and Parallel Milling:
Contour milling is layered milling along the contour of the workpiece, which is suitable for processing parts with complex contours; parallel milling is milling along parallel paths, which is suitable for processing planes or parts with simple shapes. When milling titanium parts, the appropriate milling method should be selected according to the shape of the part and the processing requirements. For titanium alloy parts with complex shapes, such as aircraft engine blades, contour milling can better ensure the contour accuracy of the parts; for flat titanium alloy parts, such as titanium alloy plates, parallel milling can improve processing efficiency.
Also Read:
- What is Shaper Machine?
- What is Lathe Machine? Main parts, Operations and Working
- Water Jet Machining – Working Principle, Advantages and Disadvantages with Application
3. CNC Turning Titanium Parts
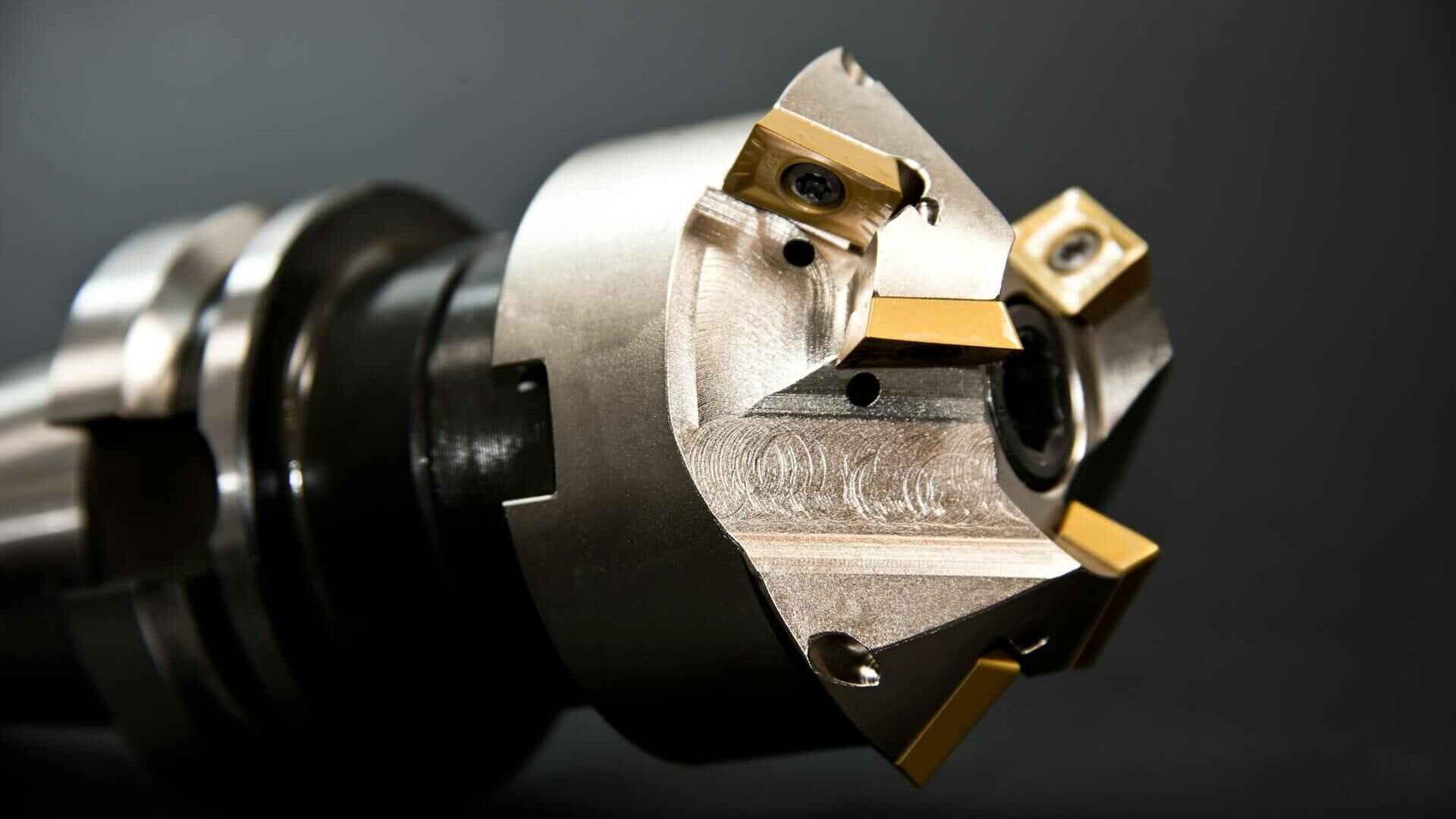
3.1 Tool Selection
Tool Material:
Similar to milling, carbide tools are widely used in CNC turning titanium parts. In addition to YG-type carbide, YW-type (general carbide) tools also have certain applications. YW-type tools combine the advantages of YG-type and YT-type (tungsten-titanium-cobalt) carbide, have good comprehensive performance, and can adapt to different processing conditions when turning titanium alloys. For example, YW1 tools can be used for semi-finishing and finishing, while YW2 tools are more suitable for roughing. In addition, ceramic tools have certain advantages in high-speed turning of titanium parts due to their high hardness, high wear resistance and good heat resistance. However, ceramic tools have poor toughness and are prone to chipping, so cutting parameters and cutting conditions need to be strictly controlled when used.
Tool Geometry Parameters:
When turning titanium parts, the rake angle of the tool is generally 5° – 10° to enhance the blade strength and reduce cutting force. The back angle is generally 8° – 12° to reduce the friction between the back face of the tool and the machined surface of the workpiece. The main deflection angle can be selected according to the shape of the workpiece and the processing requirements, and is generally between 45° – 90°. When processing slender shaft parts, in order to reduce the radial cutting force and prevent the workpiece from bending and deformation, the main deflection angle can be selected as 90°; when processing the outer circle and step surface, the main deflection angle can be selected as 45° – 75°. The rake angle is generally – 5° – 0°. The negative rake angle can make the chips flow to the surface to be processed and avoid the chips scratching the machined surface.
3.2 Cutting Parameter Optimization
Cutting Speed:
When CNC turning titanium parts, the choice of cutting speed is also limited by the characteristics of titanium alloy materials. Generally speaking, the cutting speed can be between 40 – 80m/min during rough turning, and the cutting speed can be controlled between 20 – 60m/min during fine turning. For example, when turning the outer circle of TC4 titanium alloy, the rough turning cutting speed can be selected as 60m/min, and the fine turning cutting speed can be selected as 30m/min. Too high a cutting speed will increase tool wear, increase cutting temperature, and affect processing accuracy and surface quality; too low a cutting speed will reduce processing efficiency.
Feed Rate:
The size of the feed rate directly affects the surface roughness and production efficiency of the processing. When rough turning, the feed rate can be between 0.15-0.4mm/r; when fine turning, the feed rate can be controlled between 0.05-0.2mm/r. When selecting the feed rate, the durability of the tool and the processing accuracy requirements of the workpiece need to be considered. If the feed rate is too large, the surface roughness of the processing will increase and the tool wear will accelerate; if the feed rate is too small, the processing efficiency will be reduced. For example, when fine turning titanium alloy shaft parts, in order to obtain better surface quality, the feed rate can be selected as 0.1mm/r.
Cutting Depth:
The cutting depth mainly depends on the processing allowance of the workpiece and the strength of the tool. When rough turning, if the tool and machine tool allow, a larger cutting depth should be selected as much as possible to reduce the number of passes and improve processing efficiency. Generally, the cutting depth of rough turning can be between 1-3mm; when fine turning, the cutting depth is generally between 0.1-0.5mm. For example, when turning a titanium alloy shaft, if the machining allowance is 5mm, rough turning can be performed first, with a cutting depth of 2mm and 2-3 passes; then fine turning can be performed, with a cutting depth of 0.2mm to ensure the dimensional accuracy and surface quality of the shaft.
3.3 Turning Method
External Turning:
External turning is one of the most common processing methods for CNC turning titanium parts. When performing external turning, it is necessary to reasonably select the tool and cutting parameters according to the diameter, length and processing accuracy requirements of the workpiece. For titanium alloy parts of slender shafts, due to their poor rigidity, they are prone to bending and deformation during turning. Therefore, some special process measures need to be adopted, such as using a center frame or a follower frame to increase the rigidity of the workpiece and reduce the influence of cutting force on the deformation of the workpiece. In addition, the reverse turning method can also be used, that is, turning the tool from the right end to the left end of the workpiece so that the direction of the cutting force points to the chuck, thereby reducing the bending deformation of the workpiece.
Inner Hole Turning:
Inner hole turning is mainly used to process the inner hole surface of titanium alloy parts, such as sleeves, bearing seats, etc. The difficulty of inner hole turning is relatively large because the tool is cutting inside the workpiece, and the chip removal and heat dissipation conditions are poor. In order to ensure the machining accuracy and surface quality of the inner hole, it is necessary to select appropriate tools and cutting parameters. The overhang length of the tool should be shortened as much as possible to improve the rigidity of the tool; at the same time, effective cooling and lubrication measures should be adopted, such as using high-pressure coolant to spray the coolant directly into the cutting area to reduce the cutting temperature, reduce tool wear, and improve chip removal. When processing deep holes, special deep hole processing tools and processes are also required, such as gun drills, BTA drills, etc.
Thread Turning:
When CNC turning titanium parts, thread turning is also an important processing content. Due to the low elastic modulus of titanium alloy, elastic deformation is easy to occur during thread turning, which makes it difficult to ensure the accuracy and surface quality of the thread. Therefore, when performing thread turning, it is necessary to select suitable tools and cutting parameters, and take some special process measures. The tooth angle of the tool should be consistent with the tooth angle of the thread, and the cutting edge of the tool should be sharp to reduce the cutting force. The selection of cutting parameters should take into account both processing efficiency and thread quality, and generally use lower cutting speeds and smaller feed rates. In addition, in order to improve the accuracy and surface quality of the thread, multiple passes can be used to gradually reduce the cutting depth.
4. CNC Drilling
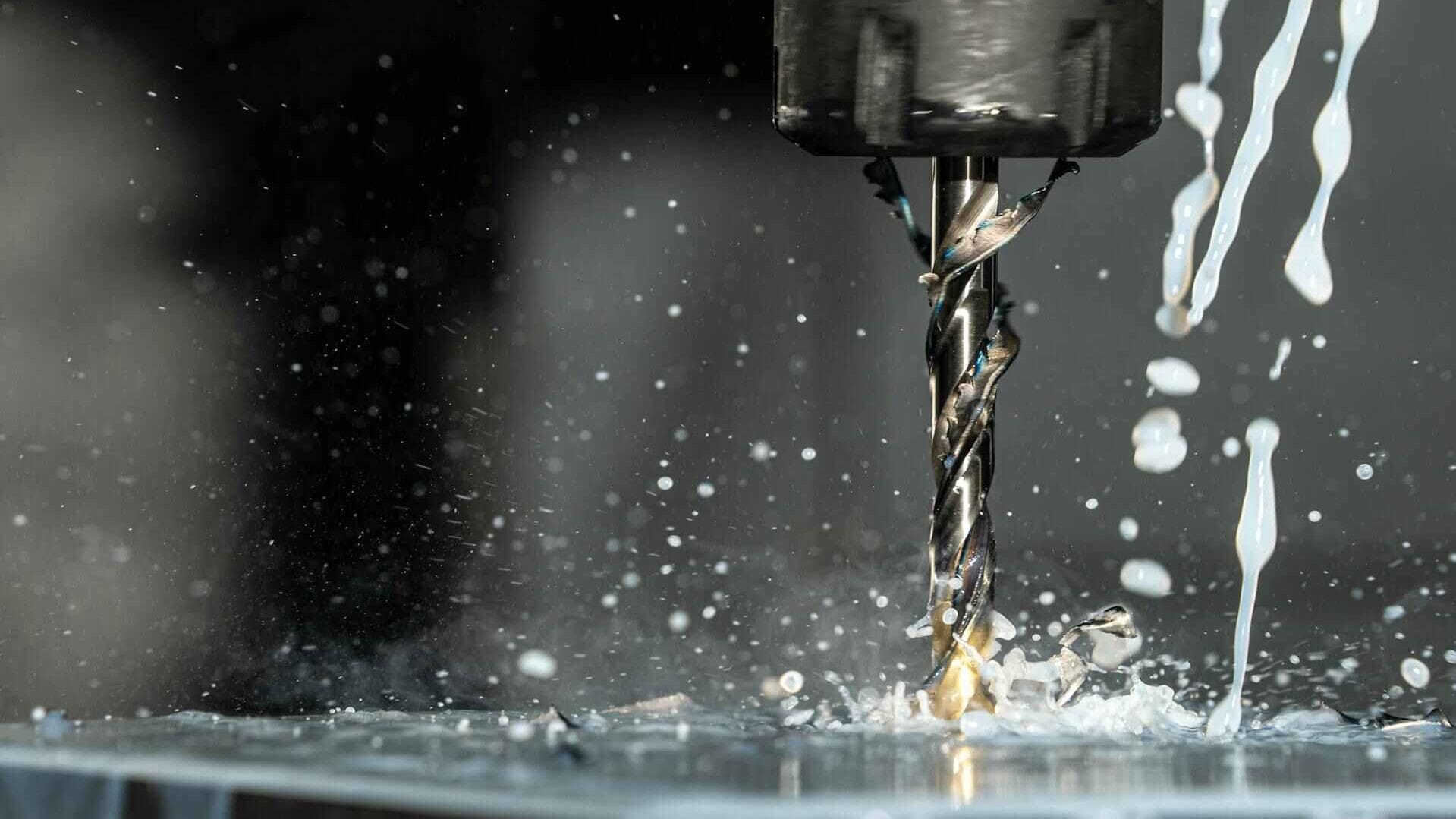
4.1 Tool selection
Tool Material:
When CNC drilling titanium parts, commonly used tool materials are high-speed steel and cemented carbide. High-speed steel tools have high toughness and bending strength. In some occasions where the processing accuracy is not high, such as shallow drilling depth and large hole diameter, high-speed steel drills still have certain applications. However, due to the poor heat resistance of high-speed steel, when processing titanium alloys, the tool wears faster and the processing efficiency is low. Therefore, for the drilling of most titanium parts, carbide drills are a better choice. Carbide has high hardness, high wear resistance and good heat resistance, which can adapt to the processing requirements of titanium alloys and improve processing efficiency and tool life. For example, YG-type carbide drills with a high cobalt content, such as YG8C, show good performance in titanium alloy drilling.
Tool Geometry Parameters:
The geometric parameters of titanium alloy drilling tools have an important influence on drilling quality and efficiency. The top angle of the drill is generally 118° – 135°. A larger top angle can make the drill better centered and reduce the deflection during drilling, but too large a top angle will also increase the cutting force and aggravate tool wear. For titanium alloy drilling, the top angle is generally selected to be around 130°. The helix angle can be between 30° and 40°. A larger helix angle is conducive to chip removal, but it will reduce the strength of the drill bit. The chisel edge width should be minimized to reduce the axial cutting force, which can generally be achieved by grinding the chisel edge. The chisel edge length after grinding can be reduced to 1/3 – 1/2 of the original, and a negative rake angle can also be ground on the chisel edge to improve cutting conditions.
4.2 Cutting Parameter Optimization
Cutting Speed:
Due to the low thermal conductivity and high chemical activity of titanium alloy, the cutting speed should not be too high when drilling, otherwise it will cause the drill bit to wear quickly or even break. Generally speaking, when CNC drilling titanium parts, the cutting speed can be controlled between 15 and 30m/min. For example, when using a carbide drill to drill TC4 titanium alloy, when the drill diameter is 10mm, the cutting speed can be selected to be around 20m/min. Too high a cutting speed will increase the cutting temperature, accelerate tool wear, and reduce drilling accuracy; too low a cutting speed will affect processing efficiency.
Feed Rate:
In actual processing, the feed rate can also be adjusted appropriately according to the sound, vibration and chip shape during the drilling process. If the chips are ribbon-shaped and the color is normal, it means that the feed rate is relatively appropriate; if the chips are too thick and blocky, it may be that the feed rate is too large and needs to be reduced; if the chips are too thin and curled, it may be that the feed rate is too small and the feed rate can be appropriately increased. At the same time, the drilling depth is also an important factor affecting the cutting parameters. For deep hole processing (the ratio of hole depth to hole diameter is greater than 5), a smaller feed rate and cutting speed are required to ensure smooth chip removal and prevent the drill from breaking.
4.3 Key Points of the Drilling Process
Pre-drilling Center Hole:
Before formal drilling, use a center drill to pre-drill the center hole, which can play a role in positioning and guiding, effectively preventing the drill from deflecting when cutting into the workpiece, and improving the position accuracy of the drilling. The diameter of the center hole is generally slightly smaller than the drill diameter, and the depth should be sufficient to guide the drill stably. For example, when drilling a hole with a diameter of 10mm, a center drill with a diameter of 3mm can be used to pre-drill the center hole with a depth of about 3-5mm.
Cooling and Lubrication:
During the drilling process of titanium alloy, the cutting heat is not easy to dissipate, which will cause the temperature of the drill to rise sharply and accelerate wear. Therefore, effective cooling and lubrication measures must be adopted. High-pressure coolant (pressure is generally 3-10MPa) can be directly sprayed into the cutting area to take away a lot of heat, and at the same time play a lubricating role to reduce the friction between the drill and the workpiece. The coolant can be a special titanium alloy cutting fluid, which has good cooling, lubrication and rust prevention properties. In addition, an internally cooled drill can also be used to transport the coolant to the cutting edge through the channel inside the drill, which has better cooling and lubrication effects, especially suitable for deep hole processing.
Pecking Drilling:
For deep holes or difficult-to-process titanium alloy materials, the pecking drilling method is adopted, that is, the drill periodically withdraws from the workpiece during the drilling process, takes the chips out of the hole, and prevents the chips from clogging in the hole, affecting the chip removal and drilling quality. The depth of each pecking depends on the drill diameter and hole depth, generally 2-5 times the drill diameter, and the withdrawal distance is about 5-10mm. For example, when drilling a hole with a diameter of 8mm and a depth of 40mm, the depth of each pecking can be set to 20mm, and the withdrawal distance can be set to 8mm.
5. CNC Tapping
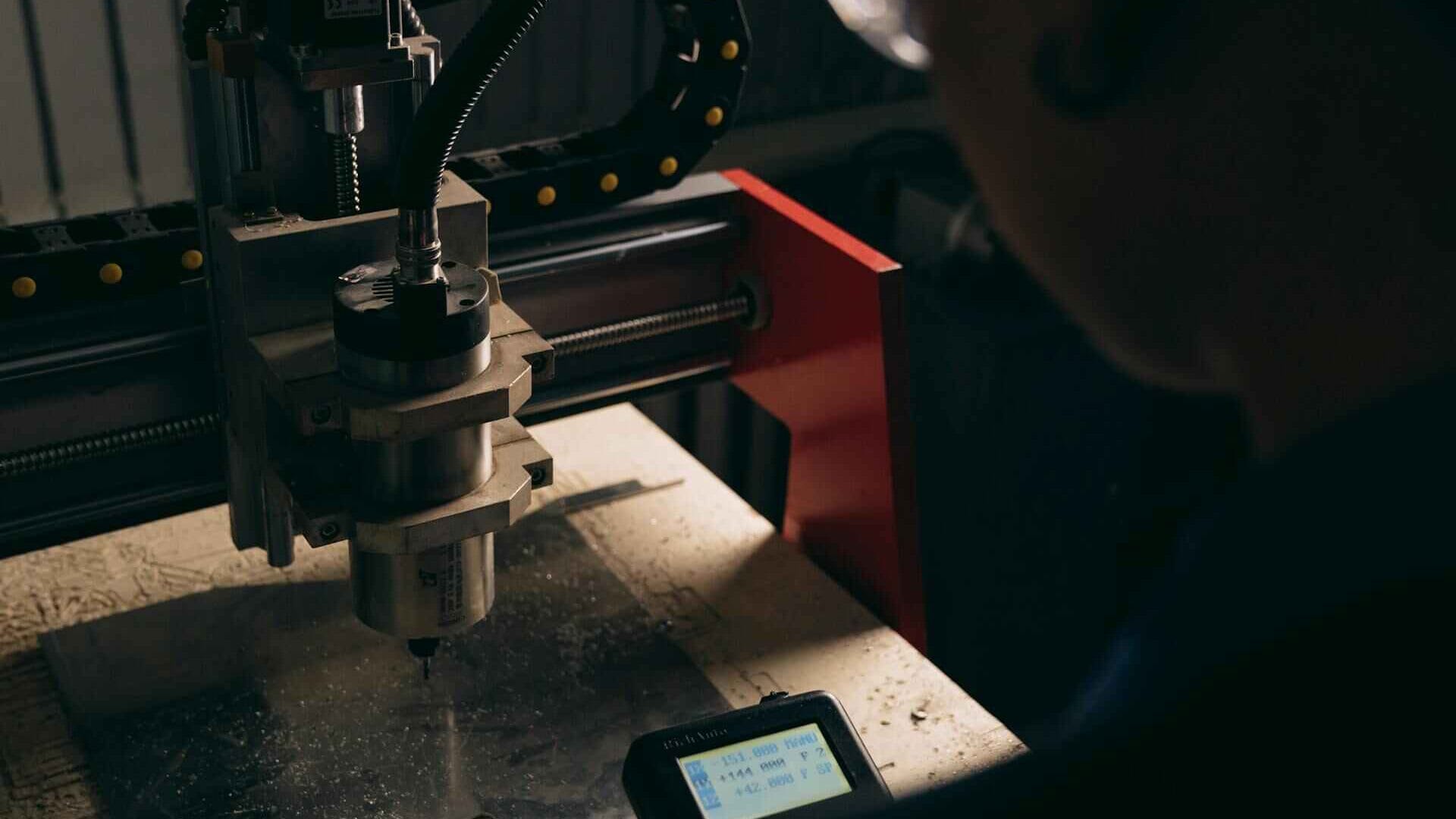
5.1 Tap Selection
Tap Material:
When machining titanium parts, the tap material needs to have good wear resistance, toughness and heat resistance. After special coating treatment (such as TiN, TiAlN coating), high-speed steel taps can significantly improve their cutting performance and service life, and are widely used in general titanium alloy tapping. Although carbide taps have high hardness and good wear resistance, they have relatively poor toughness and are easy to break. They are suitable for titanium alloy tapping with large batches, high precision requirements and low material hardness. For example, for M6 thread processing of TC4 titanium alloy, cobalt-containing high-speed steel TiAlN coated taps can be selected, which can improve processing efficiency and tap life while ensuring processing accuracy.
Tap Type:
Different types of taps can be selected according to different processing requirements. Hand taps are generally used for single-piece small-batch production or repair processing, and their accuracy is relatively low; machine taps are suitable for automated tapping of CNC machine tools, which can ensure high processing accuracy and production efficiency. In addition, there are special types of taps such as spiral groove taps and spiral tip taps. The spiral groove of the spiral groove tap can discharge the chips upward, which is suitable for blind hole tapping; the front end of the spiral tip tap has a cutting edge that can push the chips forward, which is suitable for through-hole tapping. Both taps can effectively improve chip removal and improve tapping quality.
5.2 Cutting Parameter Optimization
Cutting Speed:
Due to the poor cutting performance of titanium alloy, the cutting speed should not be too high during tapping, otherwise it is easy to cause the tap to wear more, break, and even cause problems such as thread chaos. In general, the cutting speed for tapping titanium parts is between 5 and 15m/min. For example, when tapping M8 threads on TC4 titanium alloy, the cutting speed can be selected to be around 8m/min. The specific cutting speed should also be appropriately adjusted according to factors such as the material, diameter, hardness of the workpiece, and processing batch of the tap.
Feed Rate:
The feed rate is equal to the pitch of the thread. During the tapping process, the feed rate of the machine tool must be strictly matched with the rotation speed of the tap to ensure the accuracy of the thread. For example, for an M10 thread with a pitch of 1.25mm, the feed rate should be 1.25mm/r. At the same time, attention should be paid to the accuracy of the machine tool’s feed system to avoid affecting the thread quality due to unstable feed.
5.3 Key Points of Tapping Process
Bottom Hole Processing:
The processing accuracy of the bottom hole before tapping has an important influence on the thread quality. The bottom hole diameter should be reasonably selected according to the specifications of the thread and the characteristics of the material. It can generally be calculated through empirical formulas or determined by referring to relevant manuals. For titanium alloy materials, due to its large elastic recovery, the bottom hole diameter should be slightly larger than that of ordinary materials to reduce the cutting force during tapping and prevent the tap from breaking. For example, when tapping M10 threads on titanium alloys, the bottom hole diameter can be selected as 8.8-8.9mm.
Lubrication and Cooling:
During the tapping process, good lubrication and cooling can effectively reduce the cutting force and cutting temperature, reduce tap wear, and improve the surface quality of the thread. Special tapping oil or cutting fluid containing extreme pressure additives can be used, and it can be fully applied to the surface of the tap and the bottom hole to ensure the lubrication effect. In automated processing, the cutting fluid can be sprayed into the tapping area through the cooling system of the machine tool to ensure the continuity of cooling and lubrication.
Tapping Operation:
When tapping in CNC, make sure that the tap is perpendicular to the bottom hole to avoid tap deflection, which will cause the thread accuracy to decrease or the tap to break. When starting to tap, feed slowly so that the tap can smoothly cut into the workpiece. After the tap has tapped 2-3 circles, gradually increase the feed speed. During the tapping process, if the cutting force suddenly increases or abnormal sound is heard, the processing should be stopped immediately, the tap and workpiece should be checked, and the processing can be continued only after the fault is eliminated.
6. CNC Boring
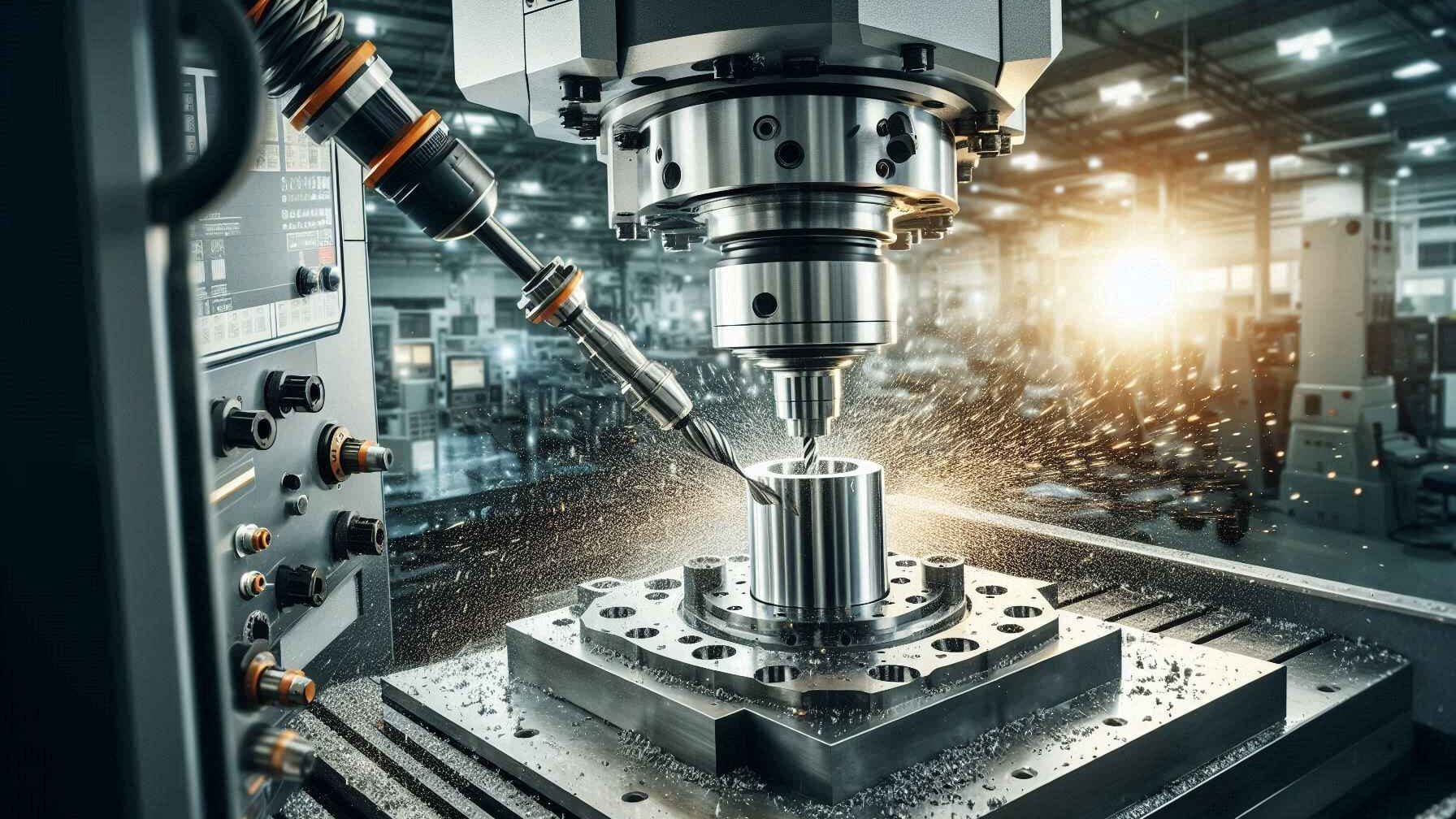
6.1 Selection of Boring Tool
Boring Tool Type:
When CNC boring titanium parts, different types of boring tools can be selected according to processing requirements. Single-edge boring tools are suitable for single-piece small-batch production and high-precision hole processing. They have a simple structure and are easy to adjust. They can accurately control the hole size through a fine-tuning mechanism. Double-edge boring tools (such as double-edge rough boring tools and double-edge fine boring tools) have good rigidity and processing efficiency and are suitable for batch production and rough and fine processing. For deep hole boring, deep hole boring tools can be used. They have a special structural design that can ensure chip removal and cooling effects during deep hole processing. In addition, there are fine-tuning boring tools, floating boring tools, etc. Fine-tuning boring tools can achieve precise hole diameter adjustment, and floating boring tools can automatically compensate for tool installation errors to improve hole processing accuracy and surface quality.
Tool Material:
Similar to other CNC machining titanium parts tools, boring tool materials can be selected from cemented carbide or coated cemented carbide. Cemented carbide boring tools have high hardness and wear resistance, and can meet the requirements of most titanium alloy boring processing. Coated cemented carbide boring tools (such as TiN, TiCN coatings) can further improve the cutting performance of the tool, reduce cutting force and cutting temperature, and extend the tool life. For example, when fine boring TC4 titanium alloy holes, using TiCN coated cemented carbide fine-tuning boring tools can achieve higher dimensional accuracy and surface quality.
6.2 Cutting Parameter Optimization
Cutting Speed:
When boring titanium parts, the selection of cutting speed should comprehensively consider factors such as tool material, workpiece material hardness, hole size and processing accuracy. Generally speaking, the cutting speed can be between 30-80m/min for rough boring, and the cutting speed can be controlled between 20-60m/min for fine boring. For example, when using a carbide boring tool to rough bore a 50mm diameter TC4 titanium alloy hole, the cutting speed can be selected as 60m/min; when fine boring, the cutting speed can be selected as 40m/min.
Feed Rate:
The size of the feed rate affects the surface roughness and processing efficiency of the bored hole. When rough boring, the feed rate can be between 0.1-0.5mm/r; when fine boring, the feed rate can be controlled between 0.05-0.2mm/r. The specific feed rate should also be adjusted according to the hole size, boring tool type and workpiece material characteristics. For example, when fine boring a small diameter (less than 20mm) titanium alloy hole, the feed rate can be selected as 0.08mm/r; when boring a large diameter (greater than 50mm) hole, the feed rate can be appropriately increased to 0.15mm/r.
Cutting Depth:
During rough boring, the cutting depth can be determined according to the machining allowance and the rigidity of the tool, generally between 1 and 3mm; during fine boring, the cutting depth is smaller, usually between 0.1 and 0.5mm. When determining the cutting depth, it is necessary to avoid vibration or damage of the tool due to excessive cutting depth, which will affect the machining accuracy and surface quality.
6.3 Key Points of Boring Process
Tool Installation and Adjustment:
The installation accuracy of the boring tool has a direct impact on the boring quality. When installing the boring tool, ensure the coaxiality of the boring tool bar and the machine tool spindle to avoid the increase of the aperture size deviation and surface roughness due to installation error. For adjustable boring tools, such as fine-tuning boring tools, they must be adjusted strictly in accordance with the operating specifications to ensure the dimensional accuracy of the tool. Before processing, a trial cut can be carried out, and the tool can be fine-tuned according to the trial cut results until the processing requirements are met.
Boring Sequence:
For multi-hole processing, a reasonable arrangement of the boring sequence can effectively reduce the deformation and processing errors of the workpiece. Generally, the principle of roughing first and then finishing, and large first and then small is followed, that is, rough boring is performed first to remove most of the machining allowance, and then finishing boring is performed; large diameter holes are processed first, and then small diameter holes are processed. At the same time, the relative position relationship between the holes should be considered to minimize the idle stroke of the tool and improve the machining efficiency.
Process Monitoring:
During the CNC boring process, parameters such as cutting force, cutting temperature and machining accuracy should be monitored in real time. Through the sensors and monitoring systems of the machine tool, abnormal conditions can be discovered in time. For example, a sudden increase in cutting force may indicate tool wear or defects in the workpiece material, and the machine should be stopped for inspection in time; excessive cutting temperature will affect the tool life and machining accuracy, and the temperature can be reduced by adjusting cutting parameters or strengthening cooling measures.
7. CNC Grinding
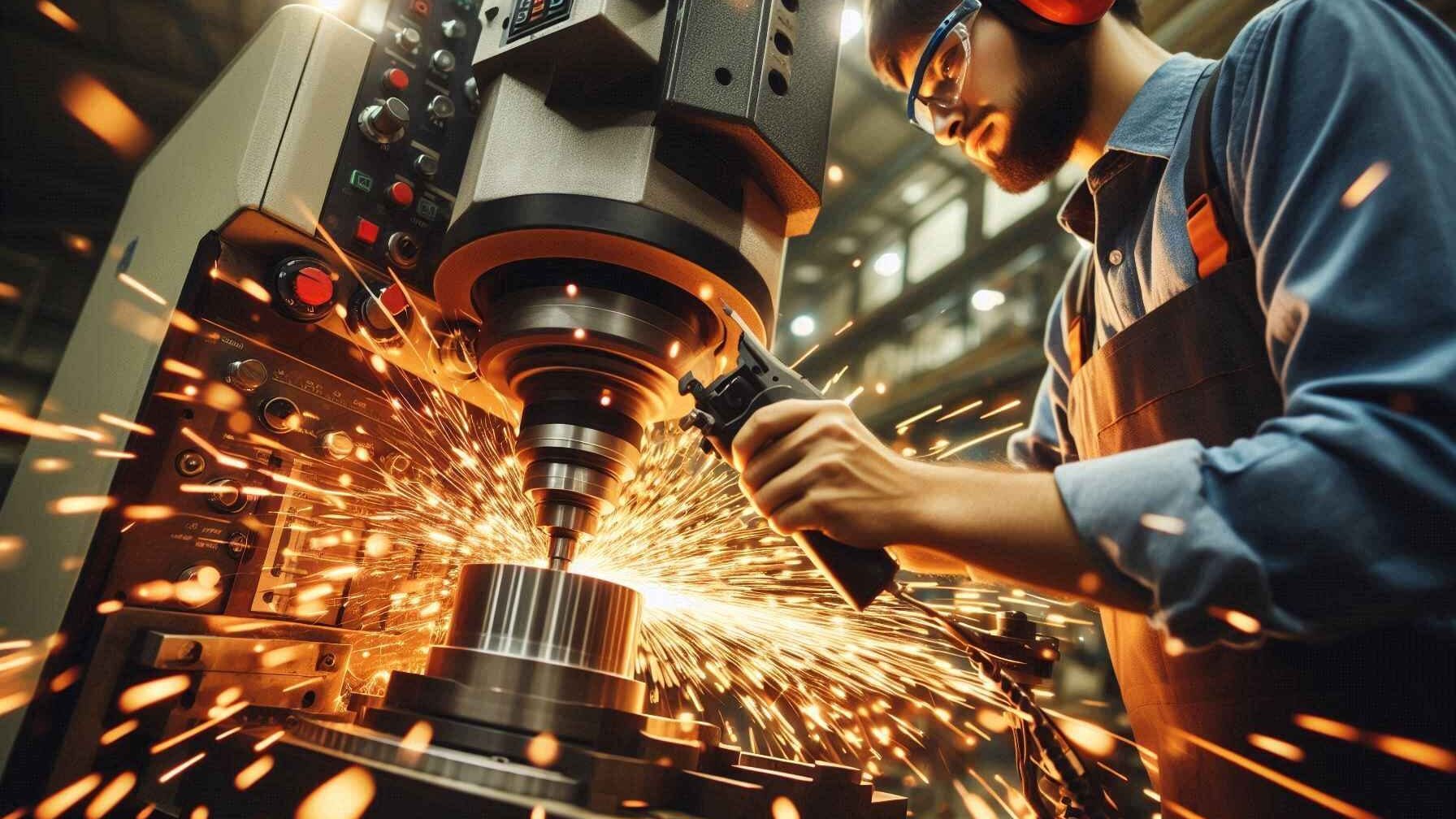
7.1 Grinding Wheel Selection
Grinding Wheel Abrasives:
When grinding titanium parts, commonly used grinding wheel abrasives are aluminum oxide and silicon carbide. Alumina grinding wheels (such as white corundum WA and brown corundum A) have good toughness and are suitable for grinding tough materials such as titanium alloys. Among them, white corundum grinding wheel has higher hardness and better cutting performance, and is suitable for fine grinding; brown corundum grinding wheel has a relatively low price and is suitable for rough grinding. Silicon carbide grinding wheel (such as green silicon carbide GC, black silicon carbide C) has higher hardness and better wear resistance, but is more brittle, and is generally used for grinding titanium alloy materials with higher hardness or for high-efficiency grinding. In addition, cubic boron nitride (CBN) grinding wheel has excellent performance in grinding titanium alloy due to its ultra-high hardness and wear resistance, which can significantly improve grinding efficiency and surface quality, but it is more expensive and is often used for high-precision, large-scale grinding.
Grinding Wheel Grit:
The choice of grinding wheel grit depends on the processing accuracy and surface quality requirements. For rough grinding, a coarser grit, such as 36-60#, can be used to improve grinding efficiency; for fine grinding, a finer grit, such as 80-120#, should be used to obtain better surface quality. For example, when rough grinding titanium alloy parts, a 60# brown corundum grinding wheel can be used; when fine grinding, a 100# white corundum grinding wheel can be used.
Grinding Wheel Hardness:
Grinding wheel hardness refers to the difficulty of abrasive grains falling off from the surface of the grinding wheel under the action of grinding force. For titanium alloy grinding, due to its large grinding force and high grinding temperature, it is easy to cause grinding wheel blockage. Therefore, softer grinding wheels are generally selected, such as medium-soft grade (ZR1, ZR2), so that blunt abrasive grains can fall off in time, revealing new sharp abrasive grains, and ensuring the cutting performance of the grinding wheel. However, the hardness of the grinding wheel cannot be too low, otherwise it will cause the grinding wheel to wear too quickly, affecting the processing accuracy and efficiency.
7.2 Grinding Parameter Optimization
Grinding Speed:
Grinding speed has an important influence on grinding quality and efficiency. When grinding titanium parts, the grinding speed is generally between 20 and 35m/s. A higher grinding speed can improve grinding efficiency, but it will increase the grinding temperature, causing burns and deformation on the workpiece surface; a lower grinding speed will reduce processing efficiency. For example, when using a CBN grinding wheel to grind TC4 titanium alloy, the grinding speed can be selected at around 30m/s; when using an ordinary alumina grinding wheel for grinding, the grinding speed can be selected at 25m/s.
Feed Rate:
The feed rate includes longitudinal feed rate and transverse feed rate. Longitudinal feed refers to the speed of the workpiece moving in the longitudinal direction relative to the grinding wheel, which is generally between 10-30m/min for rough grinding and 5-15m/min for fine grinding; transverse feed refers to the movement of the grinding wheel in the transverse direction relative to the workpiece, which is generally 0.05-0.2mm/str (per reciprocating stroke) for rough grinding and 0.01-0.05mm/str for fine grinding. Reasonable feed can ensure the grinding surface quality and processing efficiency. Too large feed can easily increase the surface roughness of the workpiece and even cause grinding cracks; too small feed will reduce processing efficiency.
Grinding Depth:
During rough grinding, the grinding depth can be between 0.01-0.05mm; during fine grinding, the grinding depth is generally between 0.002-0.01mm. The selection of grinding depth should be considered comprehensively based on factors such as the material properties of the workpiece, processing allowance and the performance of the grinding wheel. During the grinding process, it is necessary to avoid excessive grinding depth at one time to prevent damage to the workpiece and grinding wheel due to excessive grinding force and grinding temperature.
7.3 Key Points of Grinding Process
Cooling and Lubrication:
A large amount of heat will be generated during the grinding of titanium alloy. If it is not cooled in time, it is easy to cause burns on the surface of the workpiece, reduced hardness and deformation. Therefore, effective cooling measures must be adopted. A large amount of coolant (such as emulsion, synthetic cutting fluid) can be used to fully cool and lubricate the grinding area. The flow rate of the coolant is generally between 20-50L/min. At the same time, it is necessary to ensure that the coolant can be directly sprayed into the grinding area to take away heat and grinding chips. In addition, advanced cooling technologies such as high-pressure cooling and internal cooling grinding wheels can also be used to improve the cooling effect.
Grinding Wheel Dressing:
During the grinding process, the abrasive grains on the surface of the grinding wheel will gradually wear and passivate, resulting in a decrease in the cutting performance of the grinding wheel. Therefore, the grinding wheel needs to be dressed regularly to restore the sharpness and shape accuracy of the grinding wheel. Commonly used grinding wheel dressing methods include turning dressing, grinding dressing and rolling dressing. Turning dressing is to use a dressing tool (such as a diamond pen) to turn the grinding wheel to form new sharp abrasive grains on the surface of the grinding wheel; grinding dressing is to use another grinding wheel or a dressing wheel to grind the dressed grinding wheel; rolling dressing is to roll the grinding wheel surface with a roller to break the abrasive grains and expose new cutting edges.
Workpiece Clamping:
Due to the low elastic modulus of titanium alloy, it is easy to deform during the grinding process. Therefore, a reasonable workpiece clamping method is crucial. Vacuum suction cups, electromagnetic suction cups or special fixtures can be used for clamping to ensure that the workpiece is firmly clamped and accurately positioned, while minimizing the influence of clamping force on workpiece deformation. For thin-walled parts or titanium alloy parts with complex shapes, auxiliary supports or elastic clamping methods can be used to improve the rigidity and stability of the workpiece.
8. Application Fields of CNC Titanium Parts
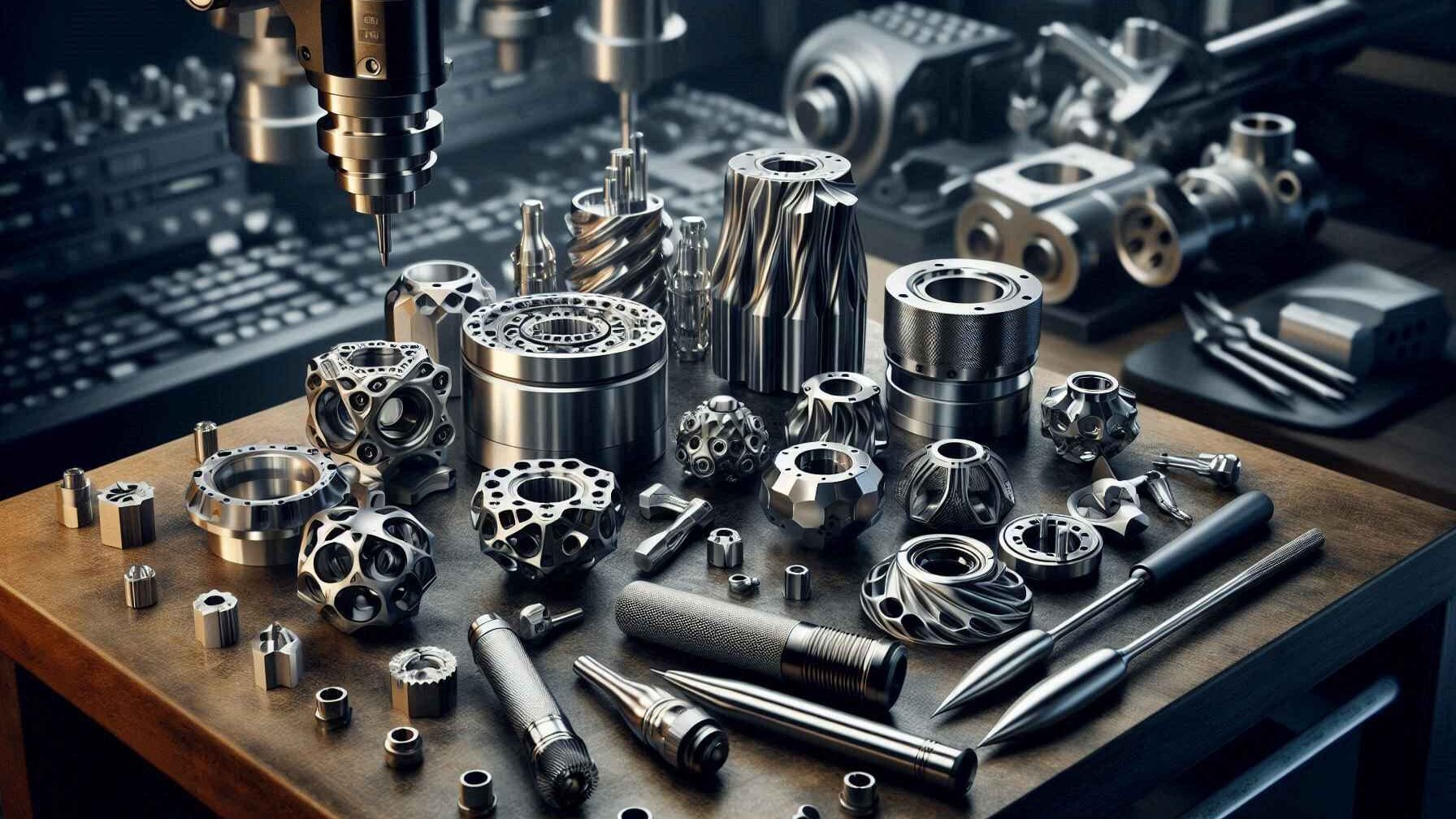
8.1 Aerospace field
Aircraft Engines:
In aircraft engines, titanium parts are widely used in key components such as compressor blades, disks, and casings. Compressor blades need to withstand high temperature, high pressure and high-speed airflow, and have extremely high requirements for material strength, high temperature resistance and fatigue resistance. CNC processing can accurately manufacture complex blade profiles to ensure their aerodynamic performance and dimensional accuracy. As one of the core components of the engine, the disk connects the blades and the shaft and needs to withstand huge centrifugal force and thermal stress. CNC processing technology can achieve high-precision processing of the disk and improve its reliability and service life. The casing is used to contain various components of the engine, and its structural strength and sealing are strictly required. CNC processing can meet the processing requirements of the complex structure of the casing and ensure the normal operation of the engine.
Fuselage Structure:
Titanium alloys are also increasingly used in aircraft fuselage structures, such as fuselage frames, skins, landing gear, etc. The fuselage frame needs to have high strength and rigidity to withstand various loads during the flight of the aircraft. CNC processing can produce high-precision frame structural parts to ensure the overall strength and stability of the fuselage. The skin directly bears the force of the air and has high requirements for surface quality and dimensional accuracy. CNC processing can achieve precise forming and processing of the skin and improve the aerodynamic performance of the aircraft. The landing gear is a key component of the aircraft during take-off and landing. It needs to withstand huge impact forces and loads. Titanium alloy landing gear can meet its high strength, high toughness and high precision requirements through CNC processing, thereby improving the safety of the aircraft.
8.2 Medical field
Implanted Devices:
Titanium and titanium alloys have become ideal materials for manufacturing human implanted devices due to their good biocompatibility, corrosion resistance and mechanical properties. Such as artificial joints (hip joints, knee joints, etc.), bone fixation devices (bone plates, screws, etc.), dental implants, etc. CNC processing can accurately produce implanted devices that conform to the human anatomical structure, ensuring their good matching with human tissues and functional realization. The surface accuracy and dimensional accuracy of artificial joints directly affect their service life and the rehabilitation effect of patients. CNC machining can achieve high-precision machining of artificial joint surfaces, reduce friction coefficients, and reduce wear. The thread accuracy and shape accuracy of bone fixation instruments are crucial to their fixation effect. CNC machining can ensure high-quality machining of bone fixation instruments and improve the success rate of fracture treatment.
Medical Equipment:
Titanium parts are also widely used in medical equipment manufacturing, such as surgical instruments and medical imaging equipment components. Surgical instruments require high strength, high hardness, corrosion resistance, and good biocompatibility. CNC machining can produce high-precision, high-performance surgical instruments to meet the strict requirements of surgical operations. Medical imaging equipment components, such as the frame of CT scanners and the magnet housing of MRI equipment, need to have good shielding performance and structural strength. Titanium alloy materials can be used through CNC machining to produce components that meet these requirements, improving the performance and stability of medical imaging equipment.
8.3 Automobile Field
Engine Parts:
In automobile engines, titanium alloys are often used to manufacture key parts such as valves, connecting rods, and crankshafts. Titanium alloy valves have the advantages of light weight, high strength, and high temperature resistance. They can reduce the reciprocating inertia force of the engine and improve the engine speed and response performance. CNC machining can accurately control the dimensional accuracy and surface quality of the valves to ensure the sealing between the valves and the valve seats. Compared with traditional steel connecting rods, titanium alloy connecting rods are much lighter, which helps to improve the fuel economy and power performance of the engine. Through CNC turning, milling and other processes, complex connecting rod structures can be processed to meet the assembly and working requirements of the engine. For crankshafts, CNC machining can ensure the dimensional accuracy, surface roughness and coaxiality of the journals, improve the reliability and durability of the crankshaft, and thus improve the overall performance of the engine.
Chassis and Suspension System:
The application of titanium alloys in automobile chassis and suspension systems is also gradually increasing. For example, the control arms, steering knuckles and other components in the suspension system are made of titanium alloy, which can effectively reduce the unsprung mass and improve the vehicle’s handling performance and driving comfort. CNC machining can achieve the precise manufacturing of complex geometric shapes of these components while ensuring their high strength and rigidity. In addition, titanium alloys can also be used to manufacture automotive exhaust system components, such as exhaust manifolds, exhaust pipes, etc. Because titanium alloys have good high temperature and corrosion resistance, they can work stably for a long time in high temperature and harsh exhaust environments, and their light weight helps to reduce the overall weight of the vehicle and improve fuel economy.
Body Structure:
In high-end automobile manufacturing, in order to pursue the ultimate lightweight and performance, some body structural parts have begun to use titanium alloys. Titanium alloy body frames can significantly reduce the weight of the body while ensuring the strength and safety of the body, and improve the acceleration performance and fuel efficiency of the vehicle. CNC machining can produce high-precision titanium alloy body frame structural parts according to the body design requirements, and assemble the components into a complete body structure through reasonable connection processes (such as welding, riveting, etc.) to meet the safety and performance standards of the car.
8.4 Other Fields
Marine Engineering:
In the marine environment, equipment needs to have excellent corrosion resistance. Titanium alloys are widely used in the field of marine engineering due to their excellent resistance to seawater corrosion. For example, the use of titanium alloys in pipes, heat exchangers, pump bodies and other parts of seawater desalination equipment can effectively extend the service life of the equipment and reduce maintenance costs. CNC machining can accurately manufacture these parts, ensure their dimensional accuracy and assembly requirements, and ensure the efficient operation of seawater desalination equipment. In addition, in the fields of marine platforms and submersibles, titanium alloys are also used to manufacture key structural components, such as the support structure of marine platforms and the pressure-resistant shell of submersibles. CNC machining technology can meet the complex processing requirements of these components, ensure their strength and sealing, and ensure the safety of marine engineering operations.
Sporting Goods:
As people’s requirements for the performance of sports goods continue to increase, the application of titanium alloys in the field of sports goods is also increasing. Such as golf club heads, bicycle frames, tennis rackets, etc. Titanium alloy golf club heads have the characteristics of light weight, high strength and good elasticity, which can improve the distance and accuracy of shots. CNC machining can produce complex club head structures, optimizing their aerodynamic performance and hitting feel. Titanium alloy bicycle frames are light and rigid, which can improve riding speed and comfort. CNC machining can accurately control the size and shape of the frame to meet different riding needs. Titanium alloy tennis rackets have good shock absorption and handling. CNC machining can ensure the quality consistency and performance stability of tennis rackets and improve the competitive level of athletes.
9. Summary
CNC machining technology provides a powerful and effective means for the manufacture of titanium parts, overcomes the difficulty of machining titanium and titanium alloy materials, and can meet the high-precision, high-quality and complex-shaped machining needs of various industries for titanium parts. In the process of CNC machining titanium parts, from CNC milling, turning, drilling, to tapping, boring, grinding and other links, tool selection, cutting parameter optimization and control of process points are all crucial. Appropriate tool materials and geometric parameters can improve the cutting performance and service life of the tool; reasonable optimization of cutting parameters can improve processing efficiency while ensuring processing quality; and strictly following the key points of each processing process is the key to ensuring the processing accuracy and surface quality of parts.
Titanium parts play an irreplaceable role in many fields such as aerospace, medical, automotive, marine engineering, and sporting goods due to their excellent performance, and their application scope continues to expand with the continuous development of technology. In the future, with the further innovation and development of CNC processing technology, such as the application of high-speed processing, five-axis linkage processing, and intelligent manufacturing, the processing of titanium parts will become more efficient, precise, and intelligent, providing more powerful support for the development of various industries and promoting the manufacturing industry to a higher level. At the same time, it is also necessary to continuously explore and research new processing technologies and methods to further improve the processing quality and production efficiency of titanium parts, reduce production costs, and meet the growing market demand.