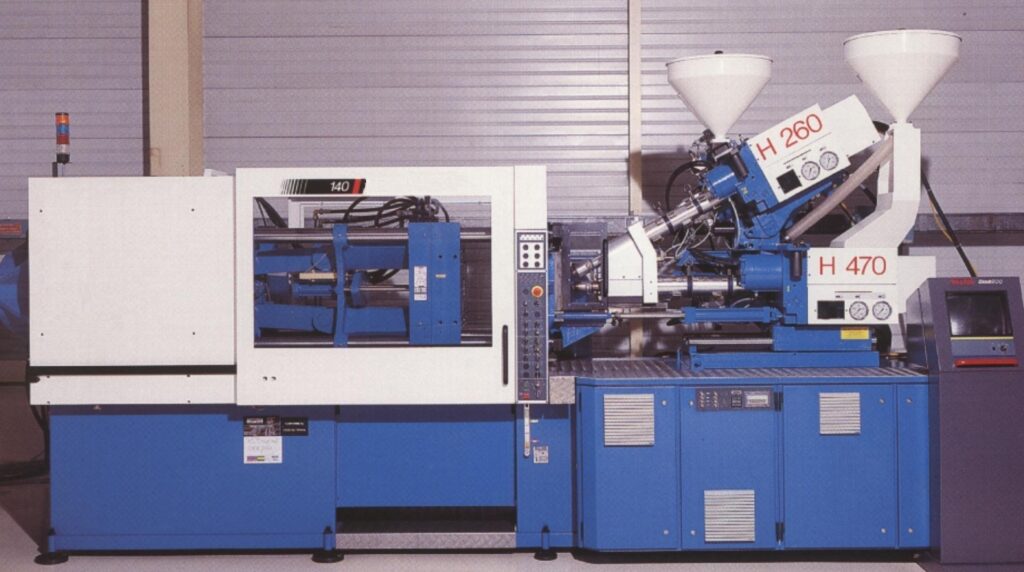
Design for Manufacturability (DFM) is a crucial aspect of the plastic injection molding process that focuses on optimizing part designs to enhance manufacturability, reduce costs, and ensure efficient production. By considering various design factors and guidelines, designers can create plastic parts that are easier to manufacture, have better functionality, and result in higher-quality end products. In this comprehensive guide, we will explore the key principles and strategies of Design for Manufacturability in plastic injection molding, empowering you to create designs that are optimized for efficient production and successful outcomes.
The Importance of Design for Manufacturability
Design for Manufacturability plays a pivotal role in the success of mold design projects. By incorporating DFM principles into the initial design stage, potential manufacturing challenges and inefficiencies can be identified and addressed early on. This not only helps streamline the production process but also minimizes the risk of costly design changes and delays later in the project timeline.
Design Considerations for Manufacturability
When designing plastic parts for injection molding, several considerations can significantly impact manufacturability. Here are key design considerations to optimize your designs for efficient production:
- Wall Thickness: Maintaining uniform and appropriate wall thickness throughout the part is essential. Thick sections can lead to longer cooling times and sink marks, while thin areas may result in warping or breakage. Strive for consistent wall thickness to ensure balanced filling, reduced cycle times, and improved part quality.
- Draft Angles: Incorporating draft angles, also known as taper, into part designs is crucial for smooth ejection from the mold. Draft angles facilitate easy release of the part from the mold cavity, reducing the risk of damage and improving overall production efficiency.
- Rib Design: Ribs are structural elements added to enhance part strength without significant increases in material usage. Proper rib design, including appropriate thickness and placement, can improve part rigidity while maintaining efficient molding and demolding.
- Fillets and Radii: Incorporating fillets and radii in sharp corners and edges can help distribute stress, minimize stress concentrations, and improve mold flow. Smooth transitions between surfaces reduce the risk of defects, such as sink marks or stress-related failures.
- Gate Placement: Proper gate placement is crucial for achieving optimal flow and filling of the mold cavity. Strategic gate placement can ensure uniform material distribution, minimize part defects, and enhance overall part quality.
- Undercuts and Side Actions: Minimizing or eliminating undercuts and complex side actions can simplify mold design and reduce manufacturing complexities. Reducing the number of moving components in the mold results in faster production cycles and increased efficiency.
Explore More
- What is Casting Defects – Types, Causes and Remedies?
- Properties of Moulding Sand in Casting
- Types of Patterns in Casting Process
Communication with Mold Manufacturers
Effective communication between designers and mold manufacturers is essential for successful Design for Manufacturability. Collaboration and feedback between these stakeholders can lead to further refinements in the design and identification of potential manufacturing challenges. Engage in open and transparent communication, leveraging the expertise of mold manufacturers to optimize designs and enhance manufacturability.
Prototyping and Testing
Prototyping and testing are integral steps in the Design for Manufacturability process. Prototypes allow for the evaluation of the part’s functionality, fit, and manufacturability. Through testing and validation, designers can identify potential design improvements and make necessary adjustments to enhance the part’s manufacturability and performance.
Continuous Improvement and Iteration
Design for Manufacturability is an iterative process that encourages continuous improvement. Learn from each project, gather feedback from the manufacturing team, and implement design modifications that optimize manufacturability and production efficiency. Strive for a collaborative environment that fosters ongoing improvement and innovation.
Conclusion
Design for Manufacturability in custom injection molding is a critical factor in ensuring efficient production, cost-effectiveness, and high-quality end products. By considering key design factors such as wall thickness, draft angles, ribs, fillets, gate placement, and communication with mold manufacturers, designers can optimize designs for manufacturability. The continuous improvement mindset and the use of prototyping and testing further refine designs and enhance the overall production process. Embrace Design for Manufacturability principles, and unlock the full potential of plastic injection molding to create exceptional parts that meet your manufacturing goals.